Energy Star 7.0 | Making Intelligent Design Decisions
Maximize operations’ bottom-line profitability and increase products’ market share by making intelligent fenestration design decisions
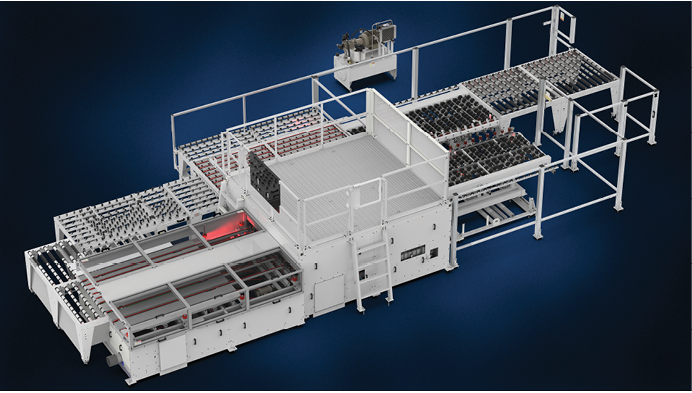
Above: GED reports its Automated Tri-Lite Assembly System (ATLAS) can produce up to three triples per minute or six doubles per minute.
Since version 7.0 of the Energy Star eligibility criteria draft was released, the industry expressed concerns about the aggressiveness of the proposed requirements, how they may impact current product designs, and the depth of the associated productivity and financial implications these changes will have on window and door manufacturing operations.
Now that Energy Star 7.0 eligibility requirements have been finalized, it is important we fully understand their impact. I will address this through this article, and others that will follow in the future. I will use comparative data analysis of existing window systems that were modeled and simulated to validate compliance with Energy Star 7.0 requirements after specific design changes have been made.
Using simulation and modeling, we debunk speculations and present a factual view of the possibilities to meet Energy Star 7.0 requirements cost-effectively, without hindering operations’ productivity.
Can we meet Energy Star 7.0 requirements using double-pane IGUs?
A lot of the industry focus recently revolved around whether triple-pane IGUs are the only way to meet the requirements. Many have attempted to answer that question. Some may have inferred that triple-pane IGUs are the only way to meet the criteria. Data adds more depth to the story.
It makes common sense that triple-pane IGUs should not be the first “go-to” option if a double-pane IGU can provide adequate performance to meet the new requirements. Triple-pane IGUs can be designed to provide exceptional thermal performance due to the presence of two IG cavities and three panes of glass. They can be the preferred choice when the products’ targeted performance cannot be met with double-pane IGUs or if the cost of making the fenestration product with double-pane IGUs exceeds that of triple-pane IGUs due to the use of special product treatments or components.
One of the trade-offs when using triples is the production time, which machinery can help address. Additional trade-offs when trying to use triples as a direct replacement for an existing window include their weight and size.
They are heavier and may require upgrades to the sash, the frame and the sash lifting components in the case of double-hung and single-hung windows. Sash and frame upgrades typically require retooling, which makes changes time-consuming and costly to manufacturers.
Our data shows that some dual-pane IGU configurations can be used to meet Energy Star 7.0 requirements.
Focus on the equal performance method
The Energy Star 7.0 eligibility criteria for the Northern climate have a prescriptive method and an equal performance method. Unlike the prescriptive method, which calls for the lowest U-value of 0.22 Btu/h-ft^2-F, the equal performance method uses both U-value and SHGC criteria to meet requirements. This distinction is especially beneficial in the case of dual-pane IGU design considerations.
Although all window components play a role in dictating a window system U-value, not all components contribute to the overall system U-value equally. Glass plays the dominant role in fenestration products’ performance. Glass manufacturing technology advancements enable us to meet the U-value and SHGC requirement of Energy Star 7.0 with double-pane IGUs. Other consideration factors are the type and concentration of noble insulating gas, spacer type, overall windows and door extrusion designs, reinforcement type(s), and whether framing members use spray foam or foam inserts selectively.
Effective product design efforts should be focused on meeting today’s challenges and energy requirements considering true and tested available technologies at the most cost-effective rational—not the challenges of a decade from now at the expense of today’s cost premiums.
This means manufacturers’ products that meet the 0.26 U-value and ≥ 0.40 SHGC are technically the same as the ones hitting the 0.22 U-value. The obvious difference lies in the cost and the amount of product and process changes required.
Windows
Climate Zone U-Factor1 SHGC2 Perscriptive
Northern ≤ 0.22 ≥ 0.17 Equivalent energy performance
= 0.23 ≥ 0.35
= 0.24 ≥ 0.35
= 0.25 ≥ 0.40
= 0.26 ≥ 0.40Source: energystar.gov / EnergyStar 7.0 residential windows requirements
Summary of data from a simulation case study
The case study used a dated, double-hung window system that existed for more than 15 years. This window system was selected because it represents a wide base of average-performance, vinyl, double-hung windows in the market.
The window system used a double-pane IGU with Intercept Ultra spacer and a passive solar control glass on surface 2 and a 4th surface low-e on surface 4. The IGU had a 5/8-inch cavity and an overall under 7/8-inch with a 95-percent argon fill.
- The IGU center of glass U-value came at 0.212 Btu/h-ft^2-F and an SHGC of 0.636.
- The overall product U-value came at 0.24 Btu/h-ft^2-F, and 0.49 SHGC, making it eligible for Energy Star 7.0.
Takeaways
- Utilize glass technology advancements to your advantage and make sure the most recent LBNL insulating glass database is used to obtain the most recent glass types.
- Using a passive solar control glass on surface 2 and a 4th surface low-e on surface 4 will yield a low U-value and a high SHGC combination that has a high probability of meeting the Northern Energy Star equivalent performance eligibility requirements.
- Choose design elements carefully to achieve Energy Star 7.0 eligibility without sacrificing manufacturing capacity or pushing the limits of production costs.
In upcoming articles, I will address other fenestration product design considerations and reveal their advantages and disadvantages, and expand on improving production efficiency for volume-centric IG production operations. This article, and the upcoming ones, are intended to serve the interest of the industry and its customers by providing manufacturers with facts that allow them to cost-effectively make the best products.