Performance Improvements in Insulating Glass Units
Elevating efficiency and unlocking superior insulation with advanced IGUs
The following is an excerpt from NGA Glass Technical Papers FB49-17 (2022) Performance Improvements in Insulating Glass Units: Cavity Gap and Insulating Gases, and FB63-19 Products for Energy Applications, available for free download at glass.org/store.
The insulating glass unit has replaced single lites of glass in all but a few areas. The basic principle of an IGU is to improve thermal performance by incorporating a gap between two or more lites of glass. A properly sized gap will reduce convection within the IGU with no effect on daylighting, thus reducing thermal transfer by as much as half. The design professional can further improve thermal performance by choosing from a variety of IGU component options, such as coated glass products with low-emissivity properties, insulating gases, multi-cavity IGUs and varying cavity gap width.
Importance of gas content
The thermal performance improvements of the IGU are dependent on the ability of the IGU to retain the insulating gas. A reduction in the concentration of insulating gas within the IGU has a linear correlation to the reduction in the thermal improvement of the unit. Gas retention within an IGU is dependent on several variables including, but not limited to:
- Permeability of the sealants used in the edge seal construction
- Permeability of the spacer
- Integrity of the bond between glass and sealants, and spacer and sealants
- Sealant bond width
- Uniformity of the sealants used in the unit construction
- Cleanliness of the glass and spacer during construction of the IGU that enables proper adhesion of sealants
- Fluctuation of internal airspace pressure due to wind loads, changes in temperature, altitude, glazing system and general environmental conditions
Thermal performance
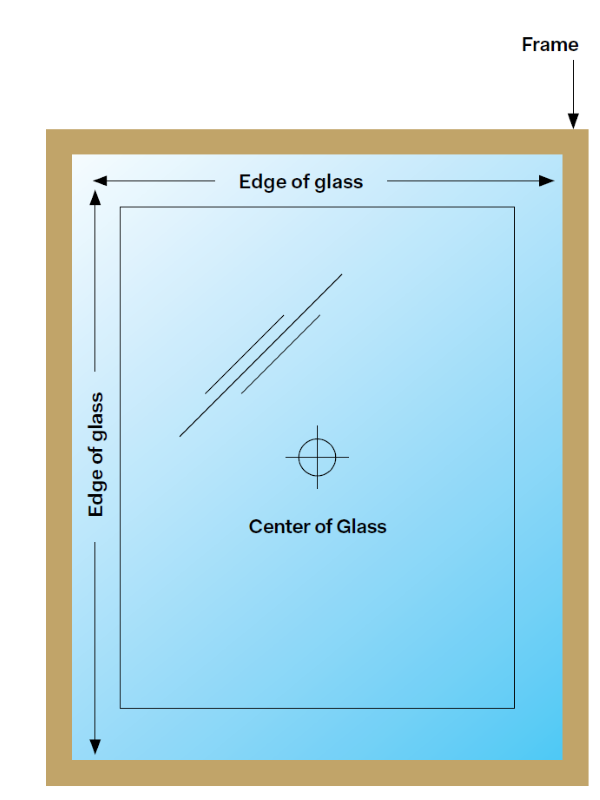
The fenestration industry measures the thermal performance of its products in terms of thermal transmission, or U-factor (also known as U-value), which is expressed in Btu/hr/ft²/°F. U-factor is a measure of the air-to-air heat transmission (loss or gain) due to the thermal transmittance resulting from the difference between indoor and outdoor temperatures. As the center-of-glass U-factor decreases, so does the amount of heat that is transferred through the IGU. The lower the U-factor, the better the product will insulate a building.
U-factor and R-value are reciprocals. For instance, dividing 1 by the U-factor will obtain the R-value for glass (for example, a 0.25 U-factor equals an R-value of 1/0.25, or 4). However, U-factors and R-values for other building materials, such as insulation, are not always directly comparable to glass.
While center-of-glass U-factors are useful for comparison in many glass products, the center-of-glass U-factors will typically be lower than the total fenestration system U-factor. Total fenestration system U-factor is calculated using thermal measurements from the center and edges of the glass, the frame and along any dividers the window/door may have (see Figure 1).
Coating type and surface location
Low-e coatings are designed to minimize the amount of ultraviolet and infrared light that can pass through glass without compromising the amount of visible light that is transmitted. There are two types of low-e coatings: passive low-e coatings and solar control low-e coatings. Passive low-e coatings are designed to maximize solar heat gain into a home to create the effect of “passive” heating and reducing reliance on artificial heating. Solar control low-e coatings are designed to limit the amount of solar heat that passes into a home for the purpose of keeping the interior cooler and reducing energy consumption related to air conditioning.
Low-e coatings are applied to various surfaces of IGUs. Passive low-e coatings function best when on the third or fourth surface (furthest away from the sun) and are typically used in heating dominated climates, while solar control low-e coatings function best when on the lite closest to the sun, typically the second surface, and are normally used in cooling dominated climates. Solar control coatings can be combined with passive coatings on the fourth surface to improve performance values. In addition, tinted substrates can be combined with low-e coatings to decrease solar heat gain and add desired aesthetics.
Insulating gases
Traditionally, an IGU is filled with air. Some inert gases are less thermally conductive than air and will lower, or improve, the U-factor of the IGU, typically in the range of 10% to 15%. Argon is the most commonly used inert gas between the lites of an IGU to improve its thermal performance. Krypton and argon-krypton mixtures are also possible. Contact the IGU fabricator for available gas mixtures.
Optimize the cavity gap
A key to proper IGU design for insulating gases is to optimize the cavity gap for the gas being used. There is an optimal spacer width for every type of low conductivity gas, which minimizes the gas convective heat transfer. This optimum gap width differs for different gas types and different weather conditions. In general, warmer weather conditions result in wider optimum gap widths. The free LBNL WINDOW computer program can be used to readily determine optimum gap widths for unique conditions. In North America, the National Fenestration Rating Council standard summer or winter environmental conditions are used in the calculation. Consult the fabricator for cavity gaps available, as spacers are only available in discrete dimensions.
Different gases have different optimal glazing space gaps based on their respective densities to reduce convection inside the IGU, while also having the greatest possible distance to reduce conduction. The typical nominal gap width dimensions are:
- For air, approximately 1/2 inch (13 millimeters)
- For argon, approximately 7/16 inch (11-12 mm)
- For krypton, approximately 5/16 inch (8 mm)
Anything greater will increase convection inside the IGU, decreasing thermal performance.
Summary
When thinking of window designs, size, substrate, tint color and other aesthetic qualities come to mind. However, low-e coatings play an equally important role and significantly affect the overall performance of a window and the total heating, lighting and cooling costs. The cavity gap size and addition of gas or coatings are designed based on the performance requirements of the building envelope. Inert gases (argon and krypton) offer lower U-factor than with air. The effect of using krypton gas in place of argon gas is more beneficial with narrower gaps than with wider gaps.
The use of multiple low-e coatings can also significantly reduce U-factor. The interrelated nature of properties like U-factor and building interior glass surface temperature means that at times performance in one aspect may need to be reduced to achieve better performance in another. In addition, choice of overall IG thickness may be a consideration based on the framing system, which can then affect gap distance, glass thickness and choice of inert gas.