Redefining Durability and Customization with Coextrusion Technology
Coextrusion technology is streamlining production and enhancing performance to meet modern architectural demands
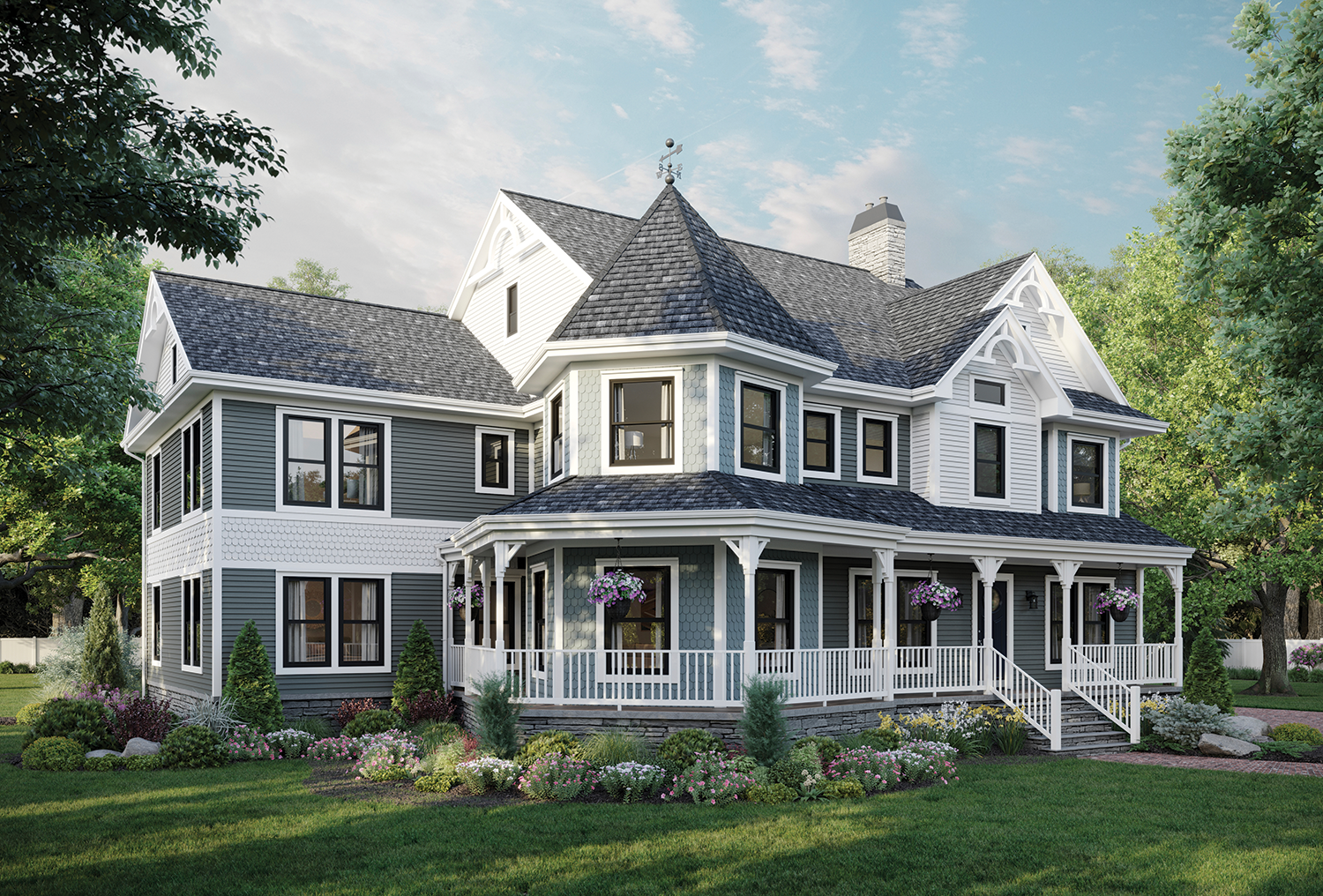
Above: Cornerstone Building Brands showcases industry innovation by leveraging coextrusion technology in product brands like Ply Gem Windows & Doors.
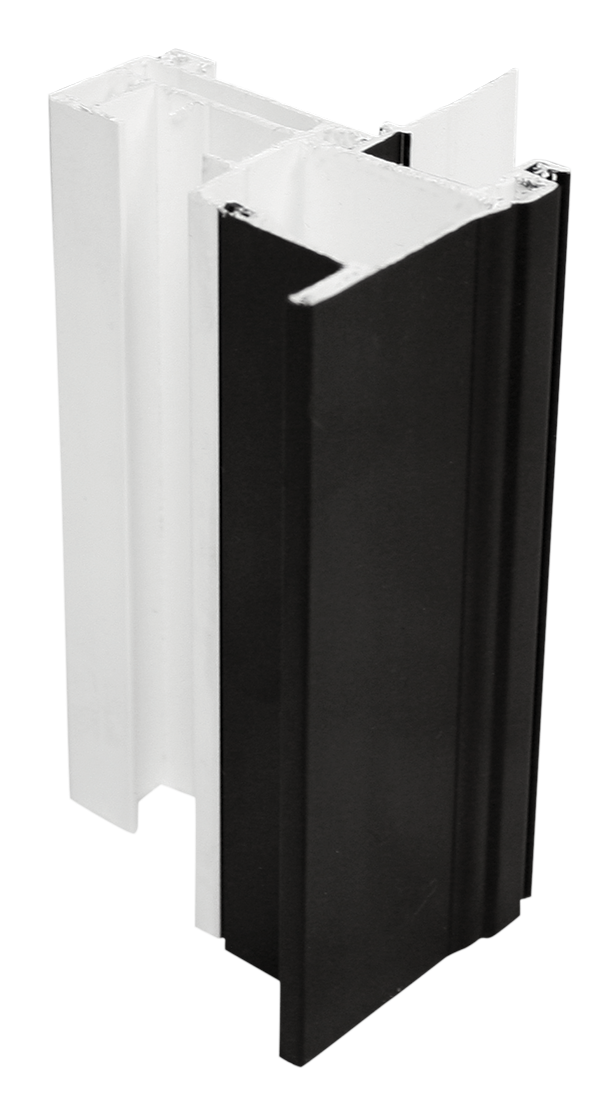
In the world of windows and doors, innovation is the name of the game. Builders, architects and homeowners demand materials that go beyond the basics—delivering durability, low maintenance and standout design. This is where coextrusion technology comes into play, offering an advanced approach that is reshaping the industry. By enabling multi-layered materials that enhance performance and aesthetics, it transforms the design, manufacturing and durability of modern windows and doors.
This article delves into this technology, highlighting its benefits and its role in helping manufacturers streamline production, reduce costs and adapt to emerging trends, all of which help ensure a competitive edge in a dynamic market.
Understanding coextrusion technology
At its core, coextrusion builds on the traditional extrusion process, where materials like polyvinyl chloride, or PVC, are shaped by pushing them through a die to form specific profiles. What sets coextrusion apart is its ability to combine multiple layers in a single pass, bonding them at a molecular level. This process integrates structural strength, weather resistance and color into the profile without requiring additional steps like painting or laminating.
The result is a unified product that resists common wear issues such as peeling or fading. Coextrusion’s efficiency and precision ensure that protective layers and finishes are built into the product during production. While painting and laminating offer benefits like customizable colors and unique textures, coextrusion can provide a complementary solution for projects that prioritize durability and shorter lead times in manufacturing.
From structural support to weather resistance and vibrant colors, coextrusion combines essential features in one streamlined process. Its ability to adapt to bold, modern design trends, like black and bronze finishes, has made it a transformative solution.
How coextrusion is adapting to market trends
In today’s construction landscape, finishing methods such as paint, laminate and coextrusion each cater to specific needs. Coextrusion, however, is gaining momentum for its ability to address the demands of modern design. As darker, bold colors such as black and bronze rise in popularity, manufacturers must address heat absorption and potential material stress.
Coextruded profiles feature protective capstock layers enriched with ultraviolet inhibitors and reflective pigments
This technology becomes even more significant for manufacturers that are vertically integrated, as it enables them to efficiently adapt to design shifts while managing production costs. By controlling key processes like coextrusion in-house, vertically integrated companies can shorten the supply chain and eliminate secondary finishing steps, such as painting or coating. This not only reduces costs but also shortens lead times since the color is built directly into the material during extrusion.
Balancing performance and production
Each finishing method offers unique strengths. Painting remains ideal for highly customized, one-off colors, while laminating is prized for its ability to add textures like woodgrain. Coextrusion, however, stands out for its seamless integration of color and durability during production. This process simplifies manufacturing, enabling quick color transitions and reducing overall production complexity.
This flexibility can make coextrusion a preferred choice for large projects requiring consistency and resilience. By providing a reliable, efficient option that can address a variety of design and performance needs, coextrusion is a valuable tool for manufacturers navigating the evolving demands of modern construction.
Future directions in coextrusion
As coextrusion technology evolves, its potential applications are expanding beyond windows and doors. Some manufacturers are working to develop even more weather-resistant materials and capstock formulations. New micro-ingredients, designed to combat fading and heat build-up, are making darker colors more viable in demanding environments.
Emerging possibilities include using coextrusion technology to incorporate components directly into the profile part. One such application is coextruding weatherstripping with the profile to create enhanced weather seals to address extreme weather conditions, such as hurricanes. These advancements demonstrate how coextrusion meets today’s needs while preparing for tomorrow’s challenges.
A comprehensive approach to design
No single method dominates the landscape of window and door manufacturing. Instead, the industry thrives on the complementary strengths of coextrusion, painting and laminating. Whether the goal is efficiency, aesthetic customization or unique surface textures, each approach plays a vital role.
By leveraging these technologies together, manufacturers continue to push the boundaries of innovation, creating building materials that are durable, adaptable and visually stunning. Coextrusion stands out for its ability to address multiple demands in a single, efficient process, making it an indispensable tool in the evolving construction landscape.